Cold plate battery cooling technology has become a mainstream solution in the new energy vehicle (NEV) industry, ensuring battery safety, performance, and longevity. Major automakers, including Tesla, BYD, NIO, and XPeng, widely adopt this technology due to its efficiency in thermal management.
Technology Variants and Adoption
The most common cold plate types in NEVs include vacuum-brazed plates (valued for high strength and sealing), friction-stir-welded plates (eco-friendly with superior weld quality), buried-tube plates (cost-effective), and deep-drilled/cavity-type plates (for high-power systems). These designs cater to different thermal and cost requirements, with Tesla and Chinese brands leading in implementation.
Performance and Challenges
Cold plates effectively regulate battery temperature by transferring heat to a coolant, preventing overheating and extending battery life. However, their added weight can impact vehicle energy density, prompting research into lightweight materials like advanced aluminum alloys. Future advancements may integrate heating and cooling for extreme climates, further optimizing efficiency.
In summary, cold plate cooling is a proven and evolving technology, balancing performance with ongoing refinements in weight and cost.
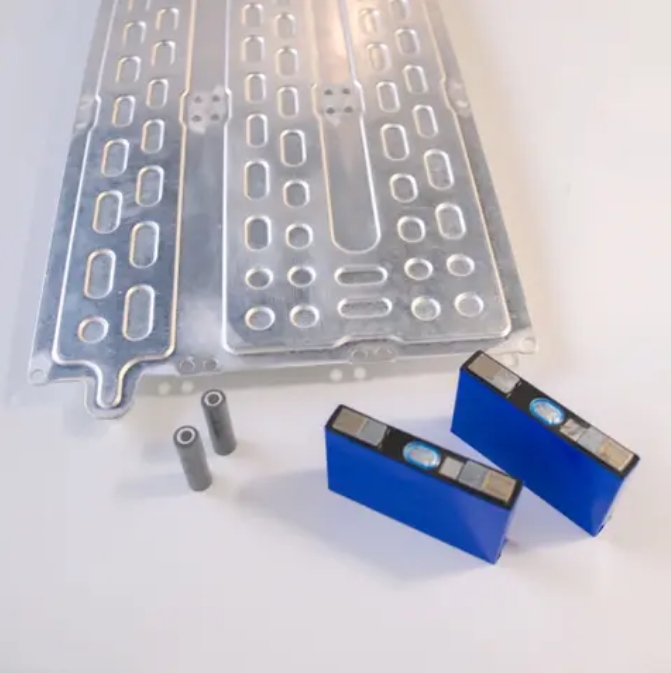